高品質な医薬品の安定供給を通じた製品価値の向上
当社では、高い品質の医薬品の安定供給に向け、生産にかかわるすべての部署が常に高い倫理観と責任感のもとに、科学的根拠に基づいた生産活動を忠実に実践しています。生産活動に関連するハード、ソフトの両面においても、医薬品を安定的に供給するための体制強化に取り組んでいます。
高品質な医薬品を安定供給するための取り組み
生命関連企業として安定的に製品を供給するためには、生産性の向上が重要です。新たに上市が見込まれる製品の生産体制については、販売開始時期や数量、製品の特性などを踏まえて構築しています。上市済みの製品についてはさらなる効率化に向け、生産体制の最適化および適切な設備投資を継続的に行っています。同時に、原薬製造から製品化まで一貫したコスト管理を行っており、製造に使用する原料および資材についても、調達先の選定段階から、徹底して管理しています。
すべての医薬品は、自社工場、外部委託会社にかかわらず、適切な品質保証体制のもとで製造しています。自社工場においては、各国GMP*1やPIC/S*2 GMPといったグローバルな規制にも準拠した品質保証体制を構築し、外部委託会社の場合は、リスクに応じた定期的な品質監査を通じて、適切な製造管理・品質管理がなされていることを確認しています。品質保証を含め製造に携わるすべての従業員に対する教育や研修、「ICH*3 Q10医薬品品質システムに関するガイドライン」に基づいた品質システムの強化、生産拠点のリスク管理体制の整備など、さまざまな施策を通じて、高品質な医薬品の安定供給に努めています。
- GMP(Good Manufacturing Practice):医薬品の製造管理および品質管理に関する基準
- PIC/S (Pharmaceutical Inspection Convention and Pharmaceutical Inspection Co-operation Scheme):医薬品分野における国際的に調和されたGMP基準および査察当局の品質システムの開発・実施・保守を目的とした査察当局間の非公式な協力組織
- ICH(International Council for Harmonisation of Technical Requirements for Pharmaceuticals for Human Use):世界各国の医薬品規制当局や製薬業界の代表者が集まり、薬事規制に関するガイドラインを作成する国際会議
品質システム
製造にかかわるすべてのプロセスで品質の確認を行いながら製造を行っています。自社が製造に使用する原材料については、製品の品質に与えるリスク(品質リスク)を評価します。また、品質リスクの高い原材料の調達先については事前の調査を行い、当社が求める品質に適合する原材料を製造できる調達先を認定企業として選定します。一度認定した調達先は品質リスクに応じて2~5年の頻度で確認を行い、適合すれば認定を継続します。選定した調達先から納入された原材料は、すべてのロットに対し自社で受入試験を行い、定めた品質基準に適合することを確認したのちに、製造に使用します。また、原料や資材については取り違え等が発生しないようにリスクアセスメントを行い、適切に管理しています。
自社の製造部門では、品質リスクに応じて、製造工程の各段階で品質の確認を行い、定められた手順に従って製造を行います。例えば、錠剤の製造工程では、錠剤の有効性や安全性に直結するような品質リスク(重量・硬度・厚み・外観など)の確認方法や頻度を、品目ごとに製造手順に規定し、適切に管理・運用しています。
また、繰り返し製造を行っても、同じ品質の医薬品が製造できるよう、製造工程の立ち上げ時にバリデーション(検証)を実施し、その結果を製造手順として規定します。また、製造に使用する設備は定期的に保守点検及び性能が維持できていることを確認しています。製造にかかわる全ての担当者は規定した手順など製造に関する教育訓練を受け、資格認定を得た者だけが製造作業を行うことができます。
生産した医薬品は、製造部門から独立した品質部門(QC部門)にて、品質の最終確認が行われます。品質確認を行うすべての担当者は、適切な品質試験が行えるのかを毎年評価され、基準に適合した者だけが、品質試験を行うことができます。医薬品の品質の確認は出荷前に行うだけでなく、出荷された医薬品の一部を参考保存品として保管し、出荷後でも品質を確認する必要が生じた場合にはいつでも指定のロットの品質を確認できる体制を整えています。また、出荷された医薬品の品質を定期的に確認する安定性モニタリングをあらかじめ指定したロットを対象に実施しており、出荷後の製品の品質に通常とは異なる傾向が確認された場合には、いつでも適切に対応できる仕組みを取り入れています。
品質部門(QA部門)では製造や試験に関わる記録の照査、変更や逸脱の管理、手順書の制定・改訂といった文書管理、教育訓練実施状況の確認などを行っています。
外部製造委託会社については、当社が求める品質に適合する医薬品を製造できることを確認する目的で品質監査を実施するとともに、品質システムや製造管理および品質管理体制を評価することによって製造委託企業として選定します。一度認定した企業も品質リスクに応じて1~4年の頻度で品質監査を行い、適合すれば認定を継続します。また、外部製造委託会社で使用する原薬は、当社で品質を評価したものを支給しています。原薬以外の原材料の品質は、品質に係る契約に基づき外部製造委託会社で評価しており、その実施状況を品質監査の中で当社が確認しています。
医薬品の偽造対策
医薬品の偽造対策として、医薬品の包装形態に応じて商品コード、有効期限や製造番号などの情報を組み込んだバーコードを表示しています。また、製品や包装材料に偽造医薬品を防止するための技術の導入にも取り組んでおり、医薬品の偽造リスクに応じた対策を検討しています。
また、偽造医薬品は出荷後の医薬品の保管管理、物流管理が脆弱な場合に正規なルート外から流通するとの考えのもとに、信頼性の高い保管及び物流を実現するためにGDP*4ガイドラインに沿った管理を行っています。医薬品の保管企業、物流企業と品質に関する契約を締結し、保管及び物流過程で発生する医薬品品質に影響する事象について迅速に対応できる体制を整えており、医療関係者や患者が当社の医薬品を安心してお使いいただけるよう努めています。更に、世界の各地域で強化が進んでいるトレーサビリティ関連の規制への対応にも取り組んでいます。
- GDP(Good Distribution Practice):医薬品の適正流通に関する基準
研修体制
工場に配属された全ての新入社員は、まずGMPの基礎や各部署の役割についての座学研修を受けます。その後、約2か月間で製造、品質試験、品質保証の現場研修を行います。そして実際に配属された部署にて実地教育を受け、習熟度に応じて、熟練者の付き添いのもとで作業ができる「レベル2」の資格、一人で作業ができる「レベル3」の資格が認定されます。
また、毎年工場の全従業員に対する教育計画を作成し、その教育計画に基づいて、薬機法・GMP省令などの法律や生産上必要な社内規則や製造・試験などの作業に必要な手順等についての教育(以降、GMP教育)を実施します。この教育計画には工場内での教育に加え、自社工場が連携した教育や信頼性保証本部による教育も含まれており、2024年度はQuality Cultureに関する教育やData Integrity教育を実施しました。なお、上記の研修とは別に、手順書を改訂した際などに必要な教育も担当者へ実施しています。
2024年度実施研修
内容 | 設定回数 | 実施した回数 |
---|---|---|
GMP教育 | 年3回以上 (担当課が年度初めに設定した回数) |
3~12回 |
Quality Cultureにおける人財育成、小野社内におけるアプローチ | 年6回 | 12回 |
GMP査察の事例教育 | 年4回 | 10回 |
Data Integrity教育 | 年2回 | 3回 |
GMP基礎教育 | 年24回 | 29回 |
手順書改訂に関する教育 | 手順書制定・改訂毎 | 2,715回 (2工場合計) |
すべての外部委託会社と締結している品質に係る契約において、従業員の教育を定期的に実施することを定めており、教育の実施状況を外部委託会社からの定期報告(1回/年)や品質監査の際に確認しています。
生産体制の強化
当社は、生産拠点としてGMPに適合したフジヤマ工場(静岡県)、山口工場(山口県)の二つの生産事業所を有しています。フジヤマ工場は、継続的に設備の改良・増強に努めています。山口工場は高活性医薬品や抗体医薬品にも対応できる注射剤製造ラインを備えており、今後の事業拡大に向けた生産能力の増強に加え、大規模災害時でも事業が継続できるよう、製品を安定供給する拠点として活用することを想定しています。
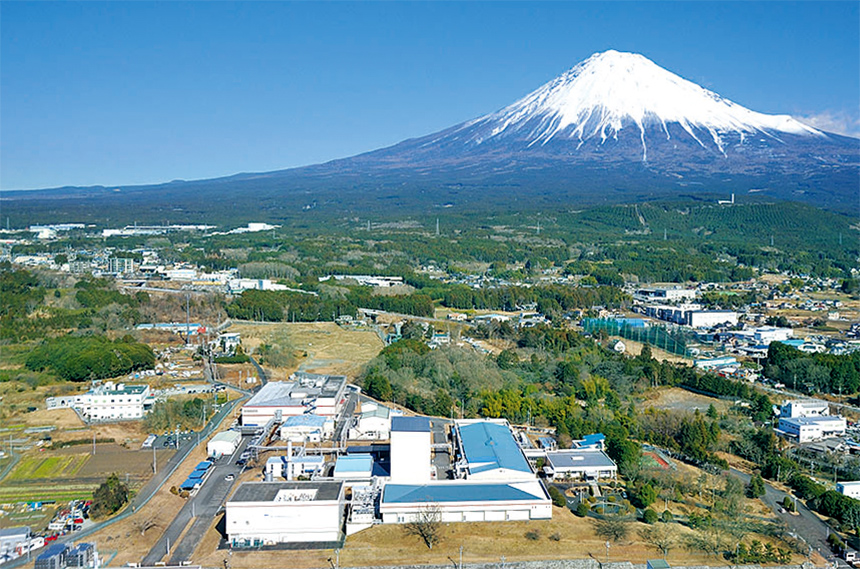
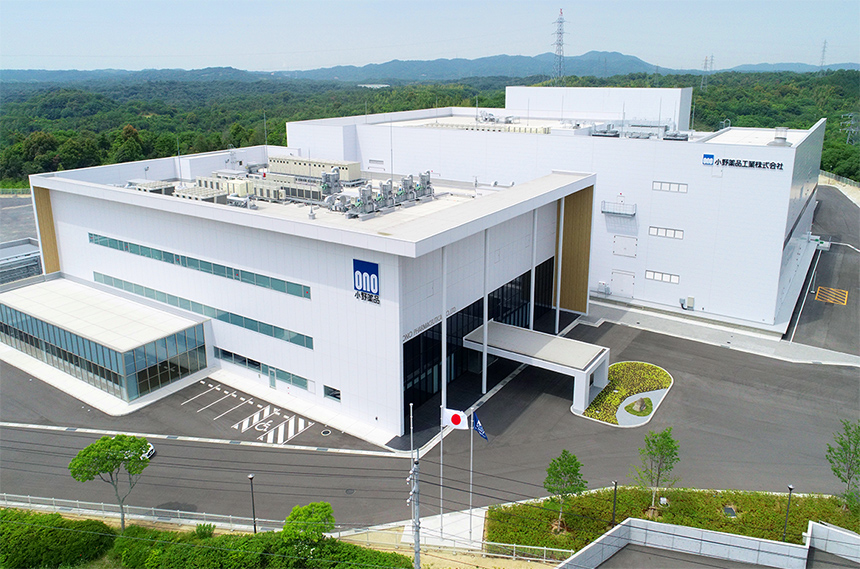
工場 | 所在地 | GMP |
---|---|---|
フジヤマ工場 | 静岡県 | 適合 |
山口工場 | 山口県 | 適合 |
2024年度はフジヤマ工場で1件、山口工場で1件の合計2件の当局のGMP調査が実施されました。いずれも重大な指摘はなく、適合の評価をもらっています。
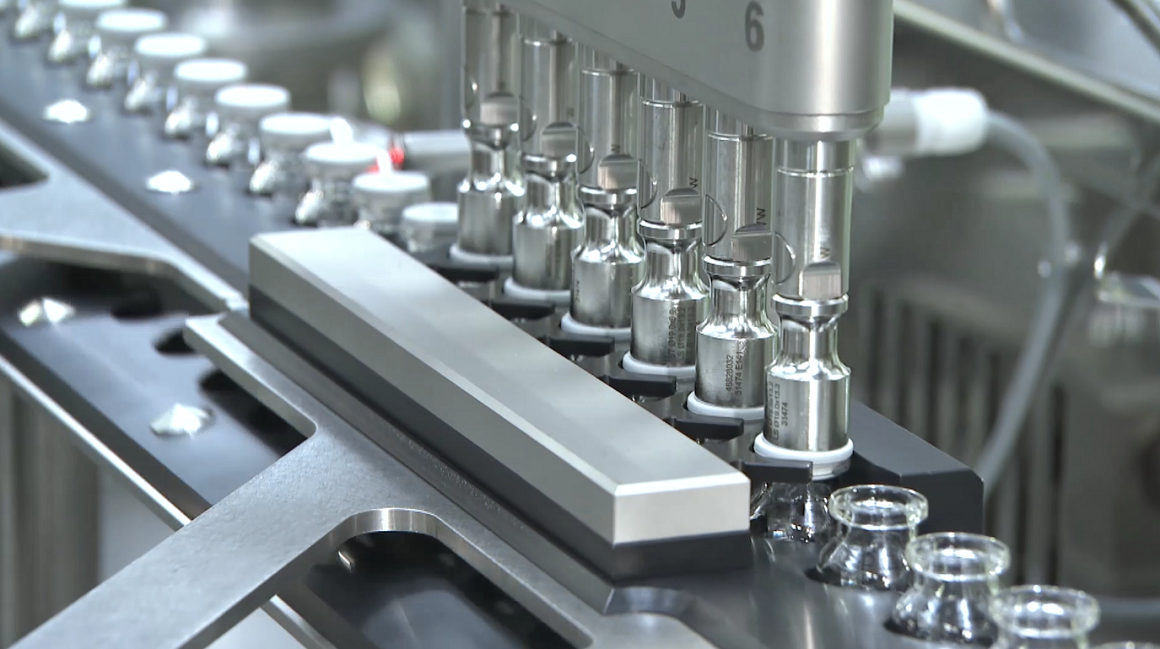