Enhancing Product Value through the Stable Supply of High-Quality Pharmaceuticals
To ensure stable supply of high-quality pharmaceuticals, all of ONO’s departments involved in manufacturing faithfully carry out scientific evidence-based manufacturing with a strong sense of responsibility and ethics. We are also working to strengthen our systems in terms of both production activity-related hardware and software in order to provide a stable supply of pharmaceuticals.
Initiatives to Ensure the Stable Supply of High-Quality Pharmaceuticals
As a company in the life sciences industry, it is essential for us to continuously improve productivity in order to maintain a stable supply of products.
We have created our production systems for products expected to be newly launched based on factors such as the timing of product launch, production volume, and product features. For products that have already hit the market, we continually strive to optimize production systems and make appropriate capital investments to further streamline our operations. Furthermore, we implement integrated cost management, from active pharmaceutical ingredient (API) production through commercialization. We also strictly manage costs of raw materials and labeling/packaging materials used in manufacturing from the supplier selection stage.
We ensure that all pharmaceuticals are manufactured, whether at in-house plants or through outsourcing companies, under appropriate quality assurance systems. All our plants have quality assurance systems in place that comply with international standards, such as GMP*1 in each country and PIC/S*2 GMP. In production at outsourcing companies, we confirm, through regular quality audits according to the risks, that appropriate manufacturing control and quality control are implemented. We take various measures to ensure a stable supply of high-quality pharmaceuticals. Such measures include providing training to all employees involved in production and quality assurance, strengthening the quality control system in accordance with the ICH*3 Q10 Pharmaceutical Quality System Guidelines, and upgrading the risk management systems at our manufacturing centers.
- GMP (Good Manufacturing Practice): Standards for manufacturing control and quality control of pharmaceuticals
- PIC/S (Pharmaceutical Inspection Convention and Pharmaceutical Inspection Co-operation Scheme): A non-binding, informal cooperative arrangement between regulatory authorities in the field of GMP of medicinal products that aims to develop, implement, and maintain internationally harmonized GMP standards and the quality systems of regulatory authorities.
- ICH (International Council for Harmonisation of Technical Requirements for Pharmaceuticals for Human Use): An international council that brings together representatives from the pharmaceutical industry and pharmaceutical regulatory authorities from around the world to develop guidelines on pharmaceutical regulations.
Quality System
We manufacture products while performing quality checks at every step of the manufacturing process. For raw materials used in our production, we assess the risks that raw materials may pose to product quality (quality risks). For suppliers of raw materials with high quality risks, we conduct prior research and only select companies who are able to produce raw materials that meet our stringent quality requirements as certified suppliers. We re-evaluate our certified suppliers at two- to five-year intervals according to the level of quality risk, and those companies are re-certified if deemed to meet our criteria. Upon receiving raw materials from our selected suppliers, we perform in-house acceptance tests for every lot, and raw materials are used in manufacture only after they are confirmed to meet the prescribed quality standards. We also perform risk assessments and appropriately manage raw materials and labeling/packaging materials used in manufacturing to prevent mix-ups and other errors.
At ONO, all products are manufactured in compliance with the prescribed procedures while checking quality at each stage of the manufacturing process according to the level of quality risk. For example, for quality testing conducted during the tablet manufacturing process, the methods and frequency of assessing the quality risks (weight, hardness, thickness, appearance, etc.) that lead directly to the tablet’s efficacy and safety are defined and documented for each item to ensure proper quality management throughout the manufacturing process.
Also, prior to beginning regular production, we conduct process validation to ensure that our manufacturing processes are capable of consistently producing pharmaceuticals of the same quality, even if the process is repeated, and we define manufacturing procedures based on the results of the validation. We periodically inspect the facilities used for production to ensure that performance is maintained. All members involved in production receive training regarding manufacturing, including the prescribed procedures, and only those who understand the procedures are allowed to be engaged in manufacturing operations.
All manufactured pharmaceuticals are subjected to final quality inspection by the Quality Control (QC) Department, which is independent from the manufacturing department. Those in charge of quality testing are evaluated every year to determine whether they can perform quality testing properly, and only those who meet the proficiency criteria are allowed to perform quality testing. In addition to checking the quality of pharmaceutical products before shipment, we store some of the shipped pharmaceuticals as reference and retention items, and even after shipment, we have a system in place that allows us to check the quality of specified lots whenever quality checks become necessary. We also conduct stability monitoring on pre-specified lots to periodically check the quality of shipped pharmaceuticals, and we have introduced a system that can respond appropriately at any time if unusual trends are found in the quality of products after shipment.
The duties of the Quality Assurance (QA) department include examination of the records related to manufacturing and testing, change and deviation management, document management, including establishment and revision of procedure manuals, and confirmation of training implementation status. In selecting contract manufacturing organizations (CMOs), we carry out quality audits on CMO candidates to confirm that they can manufacture pharmaceuticals that meet our quality standards, and we also evaluate their quality systems as well as manufacturing control and quality control systems. Only those that pass our audits are certified as our CMOs.
Certified CMOs are re-evaluated at an interval of one to four years according to the level of quality risk and are re-certified if deemed to meet our criteria. To ensure consistent quality, we supply APIs to our CMOs after conducting quality testing. As for raw materials other than APIs, their quality is evaluated by CMOs based on the relevant quality agreements. We check each CMO’s implementation status in our quality audits.
Countermeasures Against Counterfeit Pharmaceuticals
As a countermeasure against the counterfeiting our products, we incorporate information such as product codes, expiration dates, and serial numbers into its barcodes according to how pharmaceuticals are packaged. We are also working to introduce technologies to prevent counterfeit pharmaceuticals in products and packaging materials, and are considering measures according to the risk of counterfeit medicine.
In addition, based on the idea that counterfeit pharmaceuticals will be distributed from non-legitimate routes when the storage and distribution of pharmaceuticals after shipment are not managed appropriately, we manage pharmaceuticals in accordance with the GDP *4 guidelines in order to achieve highly reliable storage and distribution. We have concluded quality agreements with pharmaceutical storage companies and logistics companies, and have established a system that can quickly respond to events that affect pharmaceutical quality that occur in the storage and distribution processes, and strive to ensure that medical professionals and patients can use our pharmaceuticals with peace of mind. Furthermore, we are working to comply with traceability-related regulations that are being strengthened in various regions around the world.
- GDP (Good Distribution Practice): A standard for the proper distribution of pharmaceuticals.
Training System
New employees assigned to a plant attend lectures to learn the basics of GMP and the roles of each department, and then on-site training in manufacturing, quality testing, and quality assurance for approximately 2 months. Afterwards, they receive on-the-job training at the department to which they are actually assigned. Upon completion of the on-the-job training, depending on their proficiency level, new employees are qualified either as Level 2, which allows them to perform tasks under supervision of a skilled worker, or as Level 3, which allows them to perform tasks independently, without supervision.
We establish an annual training plan for all plant employees. Based on the plan, we conduct training sessions on the relevant laws and regulations, such as the Pharmaceutical and Medical Device Act and the GMP ordinance, the internal rules necessary for manufacturing, and the procedures required for production and testing (hereinafter referred to as “GMP training”). This plan covers not only training at plants, but also training in cooperation with plants and training conducted by the Corporate Regulatory Compliance Safety and Quality Assurance Division. In FY2024, we provided training on Quality Culture and Data Integrity. Apart from the training mentioned above, when a standard operating procedure (SOP) is revised, we provide necessary additional training to the relevant staff members.
Training held in FY2024
Content | No. of sessions scheduled | No. of sessions implemented |
---|---|---|
GMP training | At least three times a year (Scheduled by the section in charge at the start of the fiscal year) |
3 - 12 times |
Quality culture | 6 times a year | 12 times |
GMP inspection training | 4 times a year | 10 times |
Data integrity training | Twice a year | 3 times |
Basic GMP training | 24 times a year | 29 times |
Training regarding revisions of SOPs | Every time an SOP is established or revised | 2,715 times (total of two plants) |
We conclude quality agreements with all our outsourcing companies. Those agreements require them to provide regular training for their employees. We check the training implementation status through regular reports received from them (once per year) and quality audits.
Enhancement of Production Systems
We have two GMP-compliant production sites, namely our Fujiyama Plant (located in Shizuoka Prefecture) and Yamaguchi Plant (located in Yamaguchi Prefecture). The Fujiyama Plant is continuously striving to improve and enhance its facilities, while the Yamaguchi Plant is equipped with an injectable drug production line that can even handle the production of highly potent pharmaceuticals and antibody drugs. In addition to increasing production capacity for our future business expansion, we expect the Yamaguchi Plant to be used as a base for providing a stable supply of products so that our business can remain sustainable even in the event of a large-scale disaster.
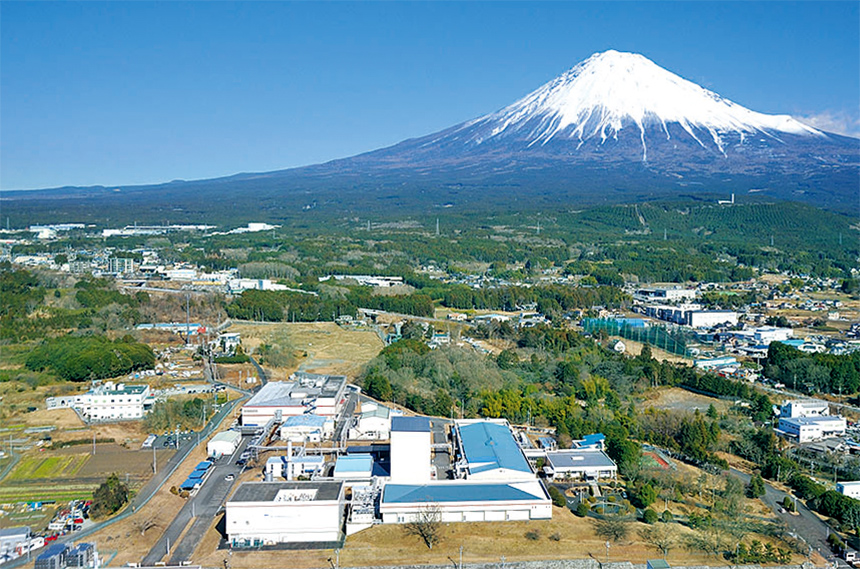
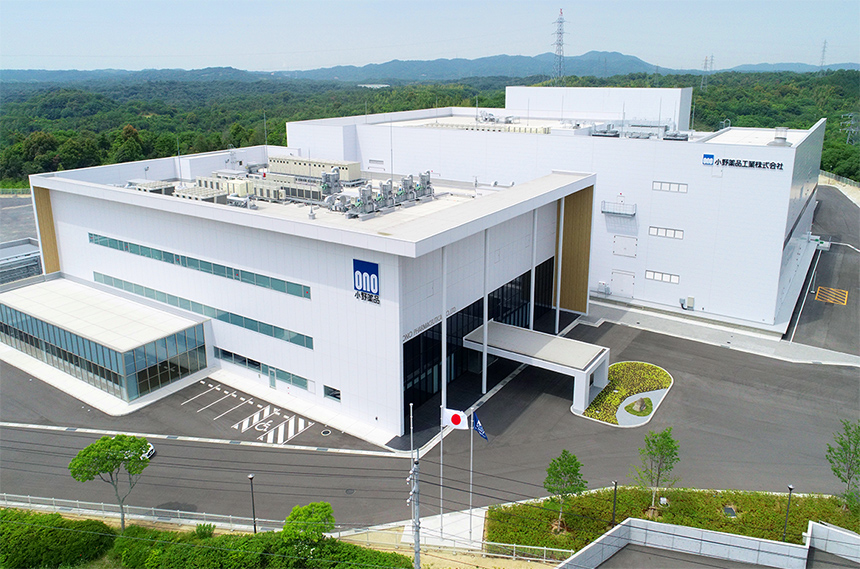
Plant | Location | GMP |
---|---|---|
Fujiyama Plant | Shizuoka Prefecture | Compliant |
Yamaguchi Plant | Yamaguchi Prefecture | Compliant |
In FY2024, a total of two regulatory GMP inspections were conducted, one at the Fujiyama Plant and one at the Yamaguchi Plant. No critical finding were reported in any of the cases, and evaluated as compliant.
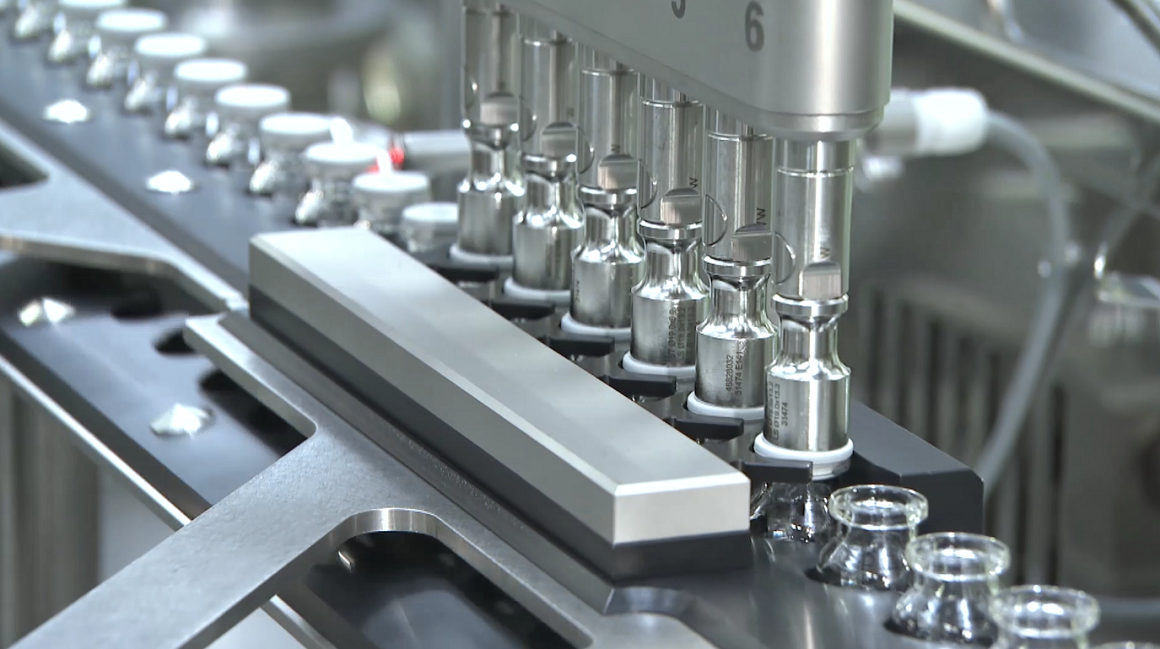